Choosing the correct medical-grade plastic for a medical device or component can be literally a “life or death” decision. Even if not that dire, selecting, then plastic-injection-molding a device that is often surgically-implanted in a human body, is qualitatively different than manufacturing a plastic toy or soda bottle cap!
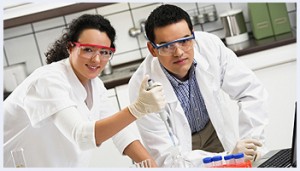
Why are plastic polymers regarded so superior to metal for medical device applications? For one very simple reason: the isotonic saline solution that constitutes the extracellular fluid in the human body tends to corrode metals but usually won’t degrade many synthetic polymers. That means an implantable artificial knee or hip joint that is made mostly of plastic will last longer, and cause fewer side-effects, than a comparable device made of metal.
Polymers are ordinarily classified into three categories:
- Thermoplastics — polymers that can be melted and molded repeatedly into an almost limitless variety of shapes.
- Thermosets — polymers that are normally rigid. They have a three-dimensional molecular network and cannot be re-melted and re-formed into another shape because they decompose rather than liquify upon re-heating.
- Elastomers — rubbery plastics that can be stretched, then spring back when the stress is released.
By far, thermoplastics are used in the vast majority of medical devices. Unlike most thermosets, thermoplastics may be melted, formed, then re-melted and re-formed again, all without significant loss of functionality.
Herewith, “The Surgical Seven”: the seven most common thermoplastics used in medical device plastic injection molding:
Polyethylene
Polyethylene can be created in high or low densities. It is impact-resistant, corrosion-resistant and water resistant. Better yet, it maintains its overall structural and performance characteristics after repeated sterilization cycles. Polyethylene is “biologically inert”, meaning it does not degrade in the body. That is perhaps the biggest reason it’s commonly used in implanted medical devices.
Polypropylene
A white polymer, polypropylene is a rugged plastic with high chemical resistance. Virtually impervious to stress, cracking, impact, and fatigue, polypropylene has a high melting point. Polypropylene is most often used to make disposable syringes, membranes for oxygenators, finger-joint prostheses, removable sutures, reusable containers, pharmacy prescription bottles and clear bags.
Polymethyl methacrylate
Polymethyl methacrylate (PMMA) is a synthetic plastic resin that features near total transparency, toughness and rigidity. An optimal substitute for glass, it can actually carry a beam of light, which is why it is frequently formed into optical fibers for endoscopy.
Polyvinyl chloride
Polyvinyl chloride (PVC) comes in two major varieties: either as a rigid or non-plastic polymer (RPVC) or as a flexible plastic. Commonly used in areas where a sterile environment is a paramount, flexible PVC is used in some applications as a substitute for rubber. PVC is dense, relatively cheap and easy to source. Rigid PVC is extremely hard and has very high tensile strength. PVC is most often used to make disposable parts for hemodialysis or hemoperfusion. It is also highly suitable for tubes, cardiac catheters, blood bags and artificial limbs.
There are other medical-grade plastics which are prevalent in this field but that’s a subject for another blog post!